The technology of making straw layers is very simple. Prepared straw tape of approximately the same size shall be glued and tight, one to another, pasted on sheets of paper (figure 4.69 b). In the preparation of tapes with them, it is desirable to remove the inner layer is the phloem, to reduce the thickness of the layer. Straw tape if they have narrowed or extended areas, it is necessary to calibrate at the same width with a ruler and scalpel. Between the lateral cut should not have notches and irregularities. The adhesive is applied a continuous layer on the reverse surface of the tape. Then tape tightly grind to a paper basis. The tape is laid, docking side surfaces, without gaps and overlays. Ready, but not dried layer should be wiped with a clean cloth, removing all traces of glue speaking.
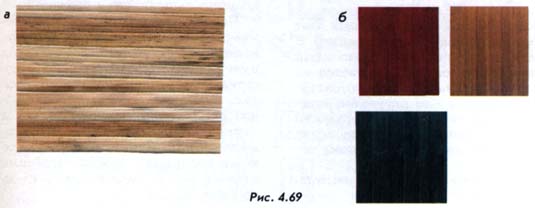
The layers are prepared, generally of straw, one tone, picking up a straw ribbon color (figure 4.69). Paper basics choose the white, not dense and without a pattern; you can use tissue paper. The thinner the paper straw and ribbon in the layers, the better the finish will look like pieces cut from them. From adhesives it is better to choose PVA: it forms a strong joint between plastic materials can be easily removed from the surface of the straw in contact with her.
During drying, the layer has not warped, it should be dried under pressure. Prepared and dried layers can be laminated with a rolling pin, resting on a solid, level surface, to give them solidity. If you work a lot in the technique of curved appliques, layers of different tones can be harvested for future use, as well as tape for a geometric application, and stored in the workplace.
As the basis on which are placed the elements of composition performed in the technique of curvilinear application, can be selected a variety of materials: wood, plywood, wood-fiber and wood-castor plates, cardboard, cloth.
Solid foundations prepared according to the General rules (see "Materials"). As a primer for wood surfaces and plates you can use stain, gouache with the addition of PVA glue, tempera. Tissue to choose a natural basis, with varying textures best suited plain cotton and linen fabrics, natural colors and painted. For the manufacture of decorative panels of fabric stretched on a frame or a base of plywood. If the fabric is the basis for decorative napkins, decorated with applique, it only cut the pattern and process edge.
Technology execution elements of decorative compositions of straw layers differs from the performance of elements of straw ribbons in a geometric application. In a curved application, each element of the composition is cut from a straw layers on prepared templates or drawings, and then on the prepared surface of all elements is a composition according to the copied sketch.
There are two ways of manufacturing elements of the layers.
The first method requires the preliminary manufacture of straw layers and templates for elements of composition. The second method can not be applied to the wall separate the layers and to produce items pre-drawn on paper, once saleeva each element separately straw ribbons.
The first method is more economical and rational in the use of straw beds. It is common among artists who are constantly engaged in curvilinear applications that perform large work. Parings and bits of straw layers, the remaining one can be used in the future. Working constantly accumulates a large palette of layers of different shades, easy to work with.
Way item sticking, though more time consuming and requires more material when working, also used by craftsmen, especially when you want to perform a small individual job or necessary in the composition to use elements not with a straight deck, and with the fan. Item gluing easier to accomplish children. As shown, children are reluctant to do layers and templates: this work takes time and postpones the date of manufacture on the item itself. When the sealing element by element the result is immediately visible in the finished element, the compositions are faster.
Figure 4.70 and shows a sketch of a flower, stylized for curved applications. The flower has a symmetrical structure about a vertical axis. In sketches that are performed for a curved application, important is the closure of all contours and clear lines. Lines which are the borders between adjacent elements should not have complex outlines.
The flower depicted in the figure meets the requirements of performance curved applications. For this example, let us consider each of the execution elements from the strata.
Performance of elements on templates. Analyze all elements in order to determine which of them will require the production pattern, and which can be manufactured by using die-cuts. In our flower (figure 4.70) most of the elements have a complex shape and only two small item in the middle of the flower has a round shape. For all the complex elements needed to produce patterns, taking into account the periodicity of the elements. All the elements will make, using die-cuts, templates for them to make not required. Without templates you can cut and small elements in the form of drops in the middle of the flower, and their size will complicate the manufacture of the template, and the form is not very complicated, not to be carved directly from the reservoir.
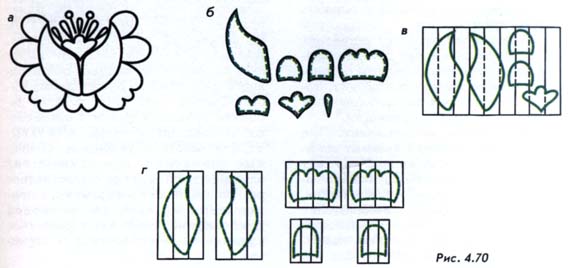
For the manufacture of symmetrical elements using a single template. The items for which you want to produce patterns shown in figure 4.70 b. For templates, you will need thick paper blocks for drawing or sketching. On paper using a carbon paper transfer alternately, dispensing at a distance from each other, the elements of the sketch. To later, when you trace the outline of the template on a straw layer, the element size is not increased by the thickness of the tip of the tool stroke, the templates should be performed to a size smaller than the actual size of the elements on the sketch (figure 4.70 b) (typically this value is 0.5—1 mm). In each case, this question is best addressed individually, knowing which tool to use for outlining contour. Figure 4.70 b solid line shows the contours of the elements, translated with a sketch, and the dashed contour cut template from a sheet of paper. If you do not make an adjustment in the size of the pattern, the distortion in the size of the elements even small, maybe in the whole volume of the composition to cause breaking proportions. In the end it may happen that the surface on which it is proposed to place the composition will be small composite spot is sprawling and does not fit within its borders.
Prepared templates imposed on straw layers from the side of the base paper, combining the direction of the flooring with the selected direction of the fibers in each element (figure 4.70). For stroke it is better to use a sharpened pencil, the contour can also be pinned or passing. In the latter two cases there may be errors and inaccuracies, particularly when transferring complex shapes and large sizes: at these ways of translation of the template into the seam edge of the elements may be damaged.
The translation templates from the paper base layer of cut elements are made in mirror image. This should be considered when applying templates to flip the mirror relative to the actual placement of the element on the sketch. In the manufacture of the pair of symmetric elements of the template also need to turn (figure 4.70) to get the mirror elements. One template is used for making all the same elements.
You can trace the templates and from the straw-flooring, this case should not be applied to the stroke of the tools that leave traces (pencil, pen). The contour pattern on the layer is transferred, peredelyvala or impaling. For displacement you can use a charged rod from a ball pen that won't leave a trace. The tool displacement should not have a thick tip, leaving a broad furrow, which will reduce the quality of the elements and the whole composition.
Item gluing. In this method, each element of the sketch is transferred through the carbon paper to the sheet of paper. The distance between the individual elements must be such that the image is free to close straw ribbons with full overlap of the contour (figure 4.70 g). After all images are transferred, the sheet of carbon paper is placed on the reverse side of a sheet of copying paper layer inside and consistently get all image elements. Thus, each image element will be repeated on the front side of the sheet and the reverse.
On the front side glued all the contours of the elements in a continuous deck (figure 4.70 g). The direction of the decking will agree with the sketch (figure 4.70 a). For drying, the sheet is placed under the press. After the glue is well dry, cut out all the elements in the contours which are drawn on the reverse side of the sheet. If used as the basis of a transparent paper type tissue, the contours on the mirror side can not be translated, because they seem to show through from the front side.
Elements performed in the technique of curvilinear of an application that can have simple and complex structure, the same element can be performed simply, or with additional decorative techniques and elements.
Figure 4.71 shows an example of various options for manufacture of sheet of the straw layer. The first sheet (figure 4.71 a) is made, the integral element of the reservoir with direct flooring. The following shows the same sheet (figure 4.71 b) made of two elements. The flooring in each element has a direction, conventionally indicating the direction of the veins on the leaf. The third sheet (figure 4.71) supplemented with scalloped edge and punching. The last leaf (figure 4.71 g) fan-made flooring. Similar changes are made on one form, make a substantial variety in its perception, and applied to the entire decorative arrangement, they will have a holistic impact on her style and character.

As already mentioned, not all elements in a curved run of an application using templates or the sealing of the circuits. To perform small elements of circular, oval and other forms, which compositions are sometimes present in large numbers, often use a variety of die-cutting. Some examples of simple elements that can be obtained with the use of the round die-cuts, shown in figure 4.72. By combining them together, you can get a large variety of decorative elements.
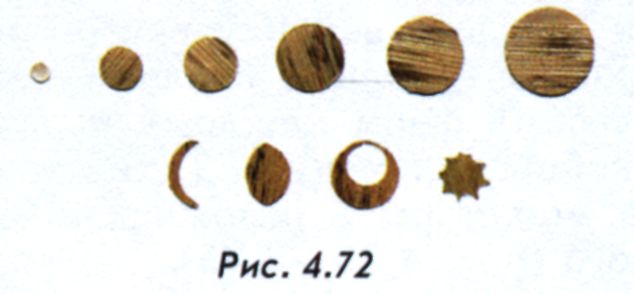
Three-dimensional elements in the application. Stick the elements onto the prepared surface can be flat or giving them a small amount. When gluing the flat element is attached to the surface of the whole plane, which is pre-lubricated with glue. When gluing the surround is glued only part of an element, typically the base of a petal or leaf. Pre elements that are voluminous, bind on the blade of the scissors sliding movement, as required in the manufacture of straw ribbons. The arc of the bend should not be too steep and prevent the item be placed freely on the plane. Can be stretched at first, the petal length, and again only some part of it: so it is possible to vary its shape and petal in this case, you will get different curves. Stick the bulk items for the end at the base. In this way can be produced as flowers convex and concave.
Volume features songs can be made of decorative elements used in the weaving of hinges, made of straw ribbons, tassels, suns, and various combinations of these elements (the technology of their production will be discussed later in the section "Straw").
Theme songs used in a curved application, repeat the theme songs of the geometric application, with the difference that the focus has shifted from ornamental and invented forms to stylized shapes and real world objects.
Being close to the natural forms, elements of composition performed in the technique of curved application, as a rule, are based on real images of flowers, herbs, leaves, birds and animals, humans, objects of nature and objects made by man. Stylization of real objects, transfers them from the reality to the world of decorative colors, shapes, lines. Styling may be a different level: can only lightly touch shape, giving it a clearer and more expressive shapes, sorting and summarizing the elements that represent the volumes in planar terms; and more in-depth work on the shape, the establishment on the basis of some new forms.